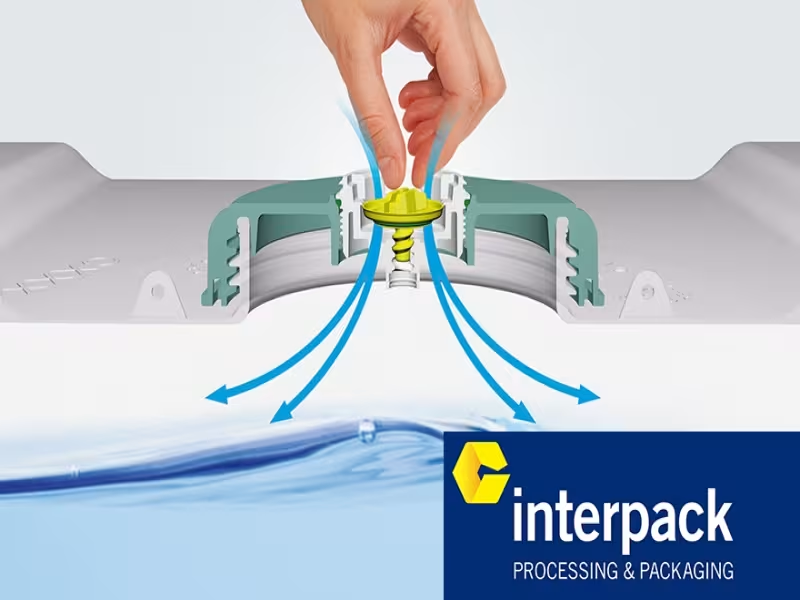
The FC / CC stopper is used to ventilate the containers quickly and safely during emptying. The Breather System allows IBCs to be emptied without having to open the screw cap.
Schütz is continuously developing and refining its IBCs and their components. At interpack 2023, the packaging specialist will be presenting the CC / FC Breather, a new ventilation system especially for IBCs of the Cleancert (CC) and Foodcert (FC) series. The company is also presenting a version of the Automatic Lock bung closure system, currently available for drums, for use in IBCs, as well as the prototype of a new 3-skid steel pallet for transporting heavy loads.
One of the main purposes of industrial packaging is to ensure the dependable protection of the filling product quality along the entire supply chain. As well as equipping containers with tamper-proof components, a key aspect is the minimisation of contamination risks, such as the introduction of particles during use. Providing components that offer smart, well-designed solutions plays a decisive role in optimising packaging standards.
New Breather System for enhanced food safety
Schütz has introduced a new standard with the CC / FC Breather, which was specially developed for the Cleancert (CC) and Foodcert (FC) product lines. At the beginning of the value chain in particular, safety and risk minimisation have the highest priority, for example in the food industry. The new CC / FC ventilation system is integrated into the bung of the screw cap that covers the IBC filling opening and it enables the user to proactively avoid contamination risks. It is used to quickly and safely ventilate the container during emptying via the bottom outlet fitting and prevents negative pressure that would cause the inner bottle to become deformed. In previous systems, either the screw cap, which is often sealed, had to be opened or the bung plug had to be removed completely with tools in an additional process step.
With the CC / FC Breather, users simply twist a screw part manually to open the venting paths in the component. This also minimises the risk of contamination during the entire emptying process. Once the container has been completely emptied, it is simply closed and the packaging is returned safely and in compliance with legal requirements. Schütz offers the system in two versions – with and without continual ventilation. Optionally, the packaging specialist can install a special membrane for transport, which additionally ensures ventilation and serves as droplet and splash protection.
Maximum protection against tampering and contamination
Another example of how Schütz helps to protect filling products is the Automatic Lock bung closure with a tamper-evident seal. This solution, already successfully established in the PE drum sector, is now also available for IBCs and will in future be supplied to IBC customers who use a screw cap with a bung as standard.
The closure system with a tamper-evident seal consists of a sealing cap and a stopper with special latching hooks. The inner sealing ring is firmly connected to the stopper, and the sealing cap is held in place by the plug. After centring, light pressure on the sealing cap makes the locking ring snap into place under the snap latches. The rigid construction ensures the lock remains securely in place once fitted. Due to the self-centring mechanism, the closure system is suitable for manual and automatic assembly. The plug cannot be opened without destroying the sealing cap. In this way, the SCHÜTZ system ensures that the originality of the filled medium is protected and preserved.
The sealing cap can be removed easily, conveniently and without tools by using the pull ring. The plastic tab connectors on the cap and the inner seal ring tear when the ring is pulled up. The snap-in hook releases the sealing cap. In the case of improper handling, preset breaking points tear, making any tampering instantly visible. Compared to metal caps, the plastic Automatic Lock sealing cap is not subject to corrosion. Especially when filling sensitive products, for example in the food or pharmaceutical industry, this supremely safe and hygienic system contributes significantly to the protection of both the contents and the people handling the container. An optional logo print on the sealing caps means that customers also benefit in terms of branding and originality.
Prototype of a new 3-skid steel pallet at interpack
Schütz is debuting another innovation as a prototype at interpack: Compared to standard steel skid pallets, the new 3-skid steel pallet has an additional middle skid, which greatly enlarges the contact area. The solution developed by Schütz offers optimised weight distribution, it is highly robust and has greatly improved handling properties on conveyor systems. Due to the high stability and minimised sagging even under full loads, the pallet is optimised for use in high-rack warehouses and automatic transport systems.
Further information about Schütz’s new products is available from May 4 to 10 at the Schütz booth D22 | E34 in Hall 10 at interpack in Düsseldorf, where all products will be exhibited and demonstrated.